How Control System Integration Saves Millions in Manufacturing Efficiency
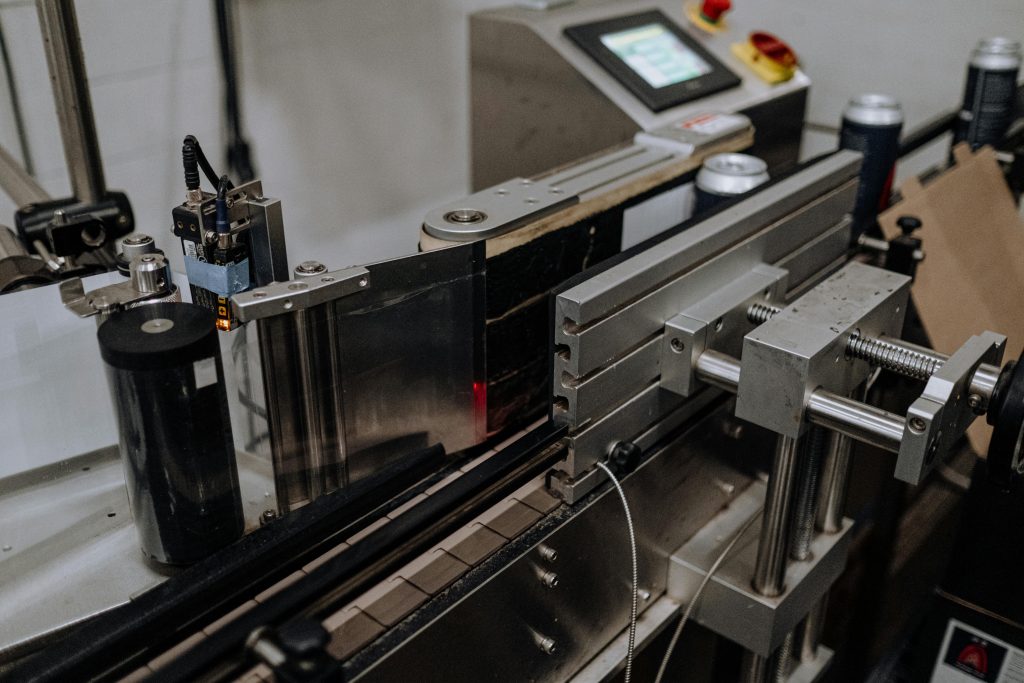
Manufacturing moves fast, and outdated systems slow everything down. The right technology doesn’t just boost production—it slashes costs, minimizes waste, and extends equipment life. Control system integration is the key to streamlining operations and keeping everything running at peak efficiency.
Is Your Factory Losing Money Due to Outdated Manual Processes?
Many factories still rely on outdated manual processes that eat into profits without anyone noticing. When machines and workers operate separately instead of as a unified system, inefficiencies pile up. Human errors, bottlenecks, and delays become costly problems that reduce overall productivity. A single miscommunication between departments or a minor manual entry mistake can lead to massive waste. Control system integration eliminates these issues by creating a centralized system where machines, software, and workers collaborate seamlessly.
With automated controls and real-time monitoring, tasks that once took hours can be completed in minutes. Production lines operate with fewer disruptions, materials are used more efficiently, and labor costs decrease as workers focus on higher-value tasks instead of manual data entry. Over time, these improvements add up, turning wasted resources into significant savings. By integrating control systems, factories stop losing money on inefficiencies and start making every minute count.
Optimizing Energy Use to Cut Costs Without Sacrificing Productivity
Energy costs are a major concern for any manufacturing operation, but reducing them doesn’t have to mean slowing down production. The key is optimizing energy use, ensuring that machines run only when needed and at peak efficiency. Control system integration plays a vital role by automatically adjusting energy consumption based on demand. Sensors, timers, and real-time analytics can track usage patterns and identify unnecessary waste, adjusting systems accordingly.
For example, smart controls can regulate lighting, ventilation, and machine power, shutting off equipment when not in use. Temperature-sensitive processes can be fine-tuned to prevent overuse of heating or cooling systems. These small adjustments lead to massive energy savings without disrupting productivity. Over time, manufacturers that implement control system integration see substantial reductions in utility costs while maintaining or even increasing output.
How Real-Time Data Tracking Reduces Downtime and Prevents Equipment Failures
Unplanned downtime is one of the biggest financial drains in manufacturing. A single machine failure can halt production, leading to missed deadlines and wasted materials. Real-time data tracking through control system integration prevents these costly interruptions by constantly monitoring equipment performance. Sensors detect fluctuations, overheating, or other early warning signs of failure, allowing maintenance teams to address issues before they cause breakdowns.
With integrated tracking, manufacturers gain instant visibility into machine health, identifying small inefficiencies before they turn into major problems. Instead of reacting to breakdowns, teams can plan repairs during scheduled maintenance windows, avoiding emergency shutdowns. The result? Higher uptime, longer-lasting equipment, and fewer production delays—saving factories millions in the long run.
Improving Worker Safety by Automating High-Risk Tasks
Manufacturing environments often come with safety risks, from exposure to hazardous materials to operating heavy machinery. Automating high-risk tasks through control system integration reduces the likelihood of workplace accidents and injuries. Robots and automated systems can handle repetitive, dangerous, or physically demanding jobs, keeping workers out of harm’s way while maintaining efficiency.
For instance, integrating automated conveyors, robotic arms, or machine vision systems eliminates the need for workers to perform manual lifting, sorting, or assembly under hazardous conditions. Additionally, smart safety systems can detect potential dangers in real time, shutting down equipment before accidents happen. This not only protects employees but also reduces downtime due to injury-related delays, keeping production lines running smoothly.
Why Predictive Maintenance Lowers Repair Costs and Extends Equipment Life
Traditional maintenance methods rely on fixed schedules or waiting for something to break before taking action. This approach leads to unnecessary repairs or costly breakdowns. Predictive maintenance, made possible through control system integration, changes the game by using real-time data to determine when equipment actually needs servicing.
By continuously monitoring vibration, temperature, and wear levels, control systems predict when components will fail before they cause problems. Instead of replacing parts too early or too late, maintenance teams can act at the perfect time—avoiding unnecessary expenses and extending the lifespan of expensive machinery. This proactive approach saves manufacturers millions in repair costs while keeping production lines running efficiently.
Scaling Manufacturing Operations Without Wasting Resources or Time
Growth brings new challenges. As production scales up, inefficiencies become more apparent, making it harder to meet increasing demand without wasting resources. Control system integration simplifies expansion by ensuring all processes remain synchronized, no matter how large the operation grows.
By automating workflows, optimizing energy use, and improving real-time data tracking, manufacturers can increase output without adding unnecessary costs. Expanding production no longer requires hiring excessive labor or overhauling existing systems—integrated controls ensure that machines, software, and employees work together seamlessly. This smart approach to scaling operations allows manufacturers to grow efficiently while keeping costs under control.