Bluing vs. Parkerizing
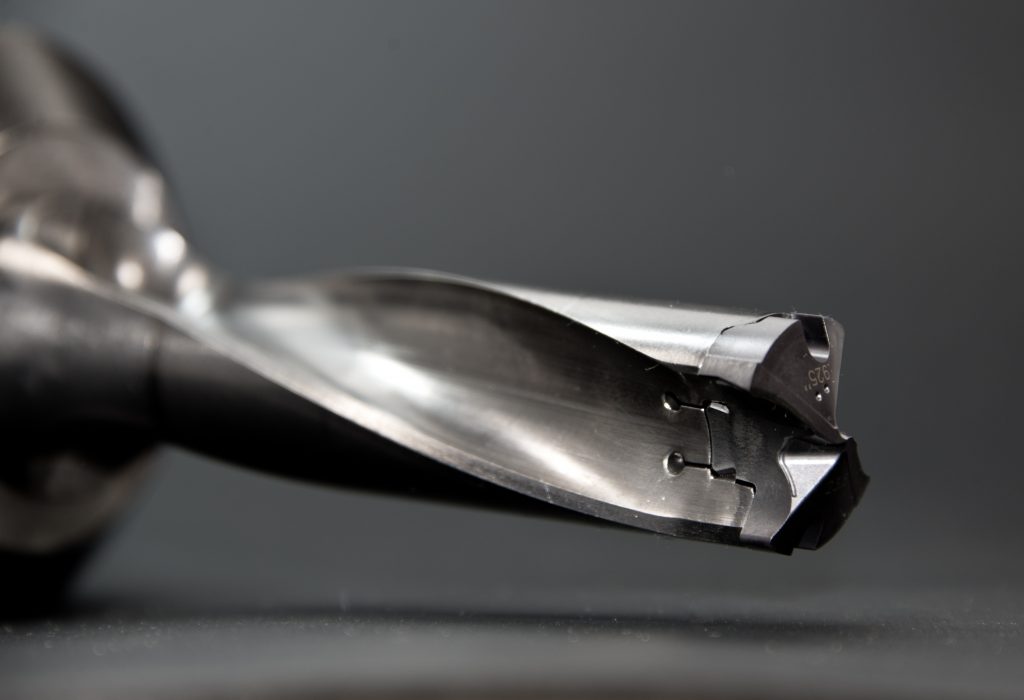
Bluing and Parkerizing are two different types of metal finishing processes.
The major difference between the two is that bluing uses heat to form a thin layer of magnetite (a type of iron oxide), while parkerizing uses electrolytes to introduce a thin layer on zinc to the surface of the metal.
Parkerizing was first used on small arms in 1905.
Bluing was first used on small arms in the late 1800s to early 1900s, but has been falling out of favor for other metal finishing processes because it may not be as durable as other systems, and have higher production costs.
The major advantage of bluing is that it penetrates the metal less than parkerizing, leaving a mirror-like finish on the metal. Bluing is usually black oxide, while parkerizing may use other colors, such as gray or dark blue.
The two processes for bluing and parkerizing are similar in that they both involve a chemical/electrical process to coat the surface of the metal.
The bluing process involves placing the metal in a salt bath of nitrates and nitrites, while the parkerizing process begins with submerging the metal into an acidic solution. The metal is then submerged into another bath that contains phosphates and other compounds to coat the surface of the metal. During this step, DC current passes through the metal, which causes zinc to plate out on the surface of the metal.
The final step of bluing is to heat treat the metal, causing magnetite to form on the surface. With parkerizing, there are multiple steps before applying heat to cause zinc phosphates to change into zinc phosphate crystals. These crystals are what provide corrosion resistance to the metal.
The major advantage of bluing is that it penetrates the metal less than parkerizing, leaving a mirror-like finish on the metal. Bluing is usually black oxide, while parkerizing may use other colors, such as gray or dark blue. This makes bluing more attractive for firearms and knives because it provides a more aesthetically pleasing finish.
Another advantage of bluing is that it forms an oxide layer much quicker than parkerizing, which makes it easier to process metal, but also decreases its corrosion resistance properties.
Parkerizing has the advantage of being much more durable because the zinc phosphate crystals are significantly harder than magnetite. This makes parkerizing more resistant to corrosion than bluing.
The main disadvantage of parkerizing is that it can leave a yellowish hue on the metal if not done correctly, while bluing leaves no color at all.
As stated earlier, bluing may be considered less durable than other metal finishing processes because its oxide layer is only about .0002-.0003 inches thick, while other processes have oxide layers that are .001 – .002 inches thick.
Both the parkerizing and bluing process can be used for items such as metal furniture, firearms, knives, and tools. However, because of the properties discussed above, the two finishes may be better suited for different applications.
After reading this article, do you think that parkerizing would better suited for protecting firearms? Find a reliable parkerizing shop near you for any parkerizing services you need.